The renewable energy market has grown in both size and importance in recent decades and continues to rapidly expand. While there is no shortage of ways to generate power, more efficient approaches are desired. One potential solution is fuel cells.

Fuel cells generate electricity through an electrochemical reaction between a fuel and an oxidizer. Hydrogen is the most common fuel and oxygen is the most common oxidizer, but other gases may be used. This reaction produces water and heat as byproducts. A fuel cell consists of a positively charged anode, a negatively charged cathode, and a membrane that allows ion exchange between the two sides. Both the anode and the cathode utilize catalysts to facilitate the reactions that occur.
While there are some hazards to transporting hydrogen and oxygen, fuel cells offer energy generation with very low emissions and the opportunity for greater efficiency than traditional combustion engines.
As the need for clean energy grows, so does the need for continual research and development. Laboratories in the private, academic, and public sectors have taken on the task. They are all aiming for the goal of maximizing energy generation to minimize carbon emissions. Significant areas of research include:
- Optimizing the fuel blend
- Finding the best catalysts to facilitate reactions at the anode and cathode, and
- Finding optimal membranes for ion exchange.
Application Requirements
In the quest for the optimal solution, instrumentation that is flexible is paramount, as many recipes must be tested in the fuel cell test stand. These include catalysts, membranes, metals, electrolytes, coatings, and electrodes. Catalysts are a key part of the recipe and are often the primary variable for any given test. All are tested under very controlled conditions, to ensure that they are operating at their most efficient state, and for much-needed repeatability. In the end, the fuel cell must consistently and reliably deliver what is promised for electrical output.
For a typical catalyst experiment, hydrogen is always on one side, and the test catalyst is on the other such as air, air plus nitrogen, air plus carbon dioxide, etc. To find the optimal chemical reaction, a wide range of gas flow rates are required.
The fuel cell test stand plays a key role in testing potential solutions. It provides control of flow, temperature and pressure for the anode and cathode gases. To ensure valid test results of each fuel cell, the test setup needs to be verified, the cell conditioned, and baseline testing conditions and operating parameters must be established. Accurate, stable gas and liquid flow control is essential to maximize stand uptime.
After testing setup has been completed, temperature, pressure, flow rates, and other operating conditions are closely monitored throughout the testing process. This information must be precisely captured, transmitted and recorded to help technicians and engineers understand how each variable influences the overall performance of the fuel cell. Digital communication protocols, particularly the high-speed EtherNet/IP and PROFINET protocols have enabled transforming data into useful knowledge.
Process Solution
A typical setup starts with the gas mixing phase with hydrogen in one tank and oxygen in another. Each tank is connected to its own valve, which then feeds into a Brooks Instrument SLA5800 mass flow controller. It boasts a wide gas flow control range of 250:1, handling extremely low to very high flow rates, giving operators flexibility to easily experiment with different reactants, using a single device. This also reduces the operator’s total cost of ownership by eliminating the need to keep spares on hand. The SLA5800 gas flow controller also features superior sensor stability or zero long-term stability. It delivers ultra-precise, repeatable output, which is critical to the validity of the process.
After the gases are mixed, they are heated and humidified. Humidification is controlled by a Brooks Instrument Quantim® Coriolis mass flow controller, which regulates the flow of ionized water. Coriolis mass flow measurement is immune to fluid property variations, making a Coriolis-type flow meter the most accurate mass flow controller. The resulting vapors are then fed into the fuel cell stack, one into the anode, the other into the cathode.
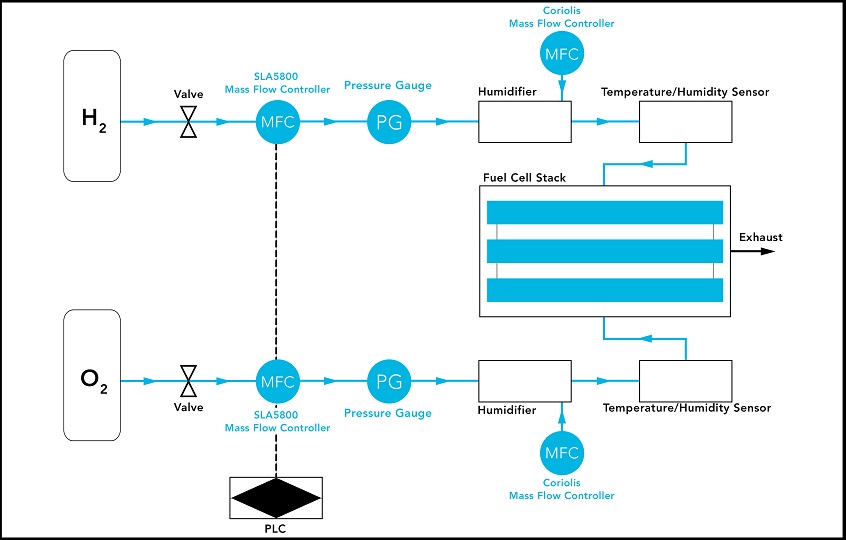
Flow Scheme
In certain cases, multiple gases are tested such as hydrogen, air, pure oxygen, carbon dioxide, and nitrogen. With the ability of the SLA5800 mass flow controller to provide real-time feedback and precise control, the technician can adjust the recipe to help achieve the optimal output. Various analog and digital communications protocols including EtherNet/IP™, PROFINET, RS-485 and several others are available with SLA5800 mass flow controllers.
Fuel cell test stands play a critical role in finding the optimal fuel blend. The process requires precision fluid flow control and accuracy which is at the cornerstone of mass flow meters supplied by Brooks Instrument.