What do the Corvette and today's new jet engines have in common (besides both going really fast)?
Answer: They both use carbon fiber materials in their construction to be lighter, more efficient and, of course, faster still.
Why, you might ask, is a flow measurement and control company like Brooks Instrument so interested in these materials?
Why Ceramic Matrix Composites (CMC)?
The material being manufactured for today's jet engines is a Ceramic Matrix Composite or CMC. The making of these CMCs require multiple gas streams during the manufacturing process.
Brooks Instrument thermal mass flow controllers are used on these gas process lines extensively throughout the entire procedure. The most common CMC configuration is a composite of tiny interwoven ceramic silicon carbon fiber embedded and intertwined in a silicon carbon-carbon ceramic matrix giving it "supernatural" capabilities. Specifically, the resultant material becomes extremely heat resistant, more so than its high-alloy metal predecessor. This ceramic material will not decompose up to 4900°F, doubling the heat resistance of the high-alloy metals. The CMC material is also lightweight as it is one third the density of conventional metal alloys used in jet engines. The "Matrix" gives the material its strength, outperforming its metal competitors.
[caption id="attachment_1737" align="alignright" width="300"]
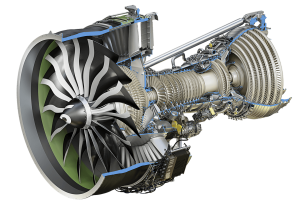
GE9X Engine Cutaway[/caption]
Manufacturing CMCs
As you can imagine, manufacturing a complex material like this comes with its challenges. And that's where our latest advancement in mass flow technology delivers thousands of dollars of savings in process downtime.
Our
GF40 Series and
GF80 Series mass flow controllers are used for the "standard" gas streams like N
2 (nitrogen), CO
2 (carbon dioxide) and other purge gases. These gas lines make up most of the processing gas for manufacturing. There are, however, a couple of major process gases used that present particular complications. These gases, also, are essential to the success of the final product.
The two gases in question are BCL3 (boron trichloride) and SiCL3 (trichlorosilane) which are used as precursor material during Chemical Vapor Infiltration (CVI), an integral part of the creation of a CMC. These gases pose inherent risk during the process as they have low vapor pressures meaning they want to be a liquid most of the time. Additionally, they are difficult to manage as they react quickly with moisture in the air to create a corrosive concoction. They must be tightly monitored and controlled to avoid failure in the process. The accuracy of the thermal mass flow controllers (MFCs) used with these two gases must be carefully scrutinized requiring regular and frequent process shutdown and MFC flow verification. This can cost upwards of $10K per hour.
Here is where the Brooks solution is realized. We have a product designed to enable in-situ gas flow verification with no need to shut down the process for MFC health checks. The
GF135 Series supplies continuous process flow data during the entire process using an on-board ROD (Rate of Decay) secondary flow measurement. The user can take advantage of:
- Enhanced process gas accuracy
- Market leading pressure transient performance, and
- MFC health indicators such as automatic trending of sensor stability and valve performance/shutdown (leak-by)
Each
GF135 is gas specific and proven on the actual gas it is set up for - no guessing or inferences here. We know it works because we brought in the gases to our lab and used them for proof positive. The
GF135 saves time and money and is the only product of its kind in the industry. And it simplifies the process!
[caption id="attachment_1735" align="aligncenter" width="300"]
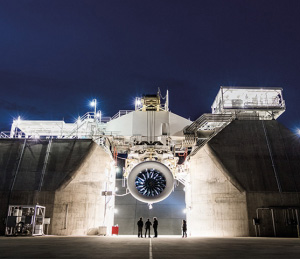
GE9X Commercial Aircraft Engine[/caption]
CMCs are expensive to make so cost cutting is important and in demand in the industry. The
GF135 is the solution for BCL3 and SiCL3 gases however it can also be used on other difficult to manage gases used in the process of making CMCs like NH3 (Ammonia).
So what's next in our world of innovation? Warp Drive perhaps? Doesn't this
GE9X CMC laden jet engine manufactured by
GE Aviation look like the Starship Enterprise?
Component datasource missing. Select a datasource for this component.